I) BLOW FILM
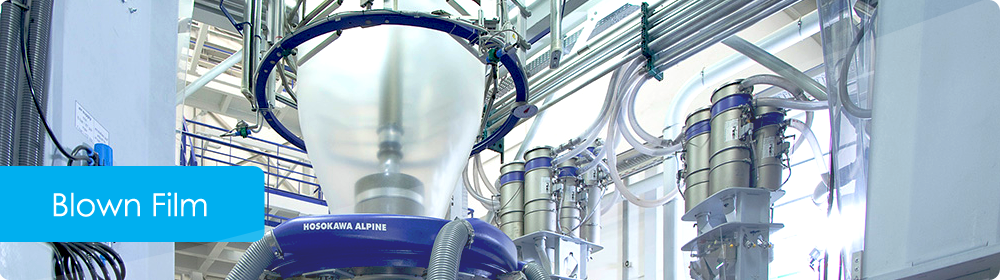
To manufacture bags, industry uses a process known as Blown Film Extrusion. This process is used to manufacture not only garbage bags but also items such as; vapor barrier, bread bags, grocery bags, or any one of thousands of different items that you would see packaged for resale.
The plastic is fed in pellet form into the machine hopper (this machine is known as an Extruder), the plastic is conveyed forward by a rotating screw inside a heated barrel and softened by both friction and heat. The softened plastic is then forced upwards through a circular die in a shape of a hollow tube.
This is a continuous process where the tube is expanded with air above the die, and collapsed by the take-off or nip rollers, the volume of air inside the bubble, the speed of the nip rollers and the extruders output rate all play a role in determining the thickness and size of the film.
The tube or “web” of film is then continuously rolled up by take-off rollers, or the web of film may be fed directly into a bag-machine in an in-line process. The tube is heat-sealed across its width to form the bottom of the bag and cut across further up the tube to form the opening.
II) INJECTION MODLING
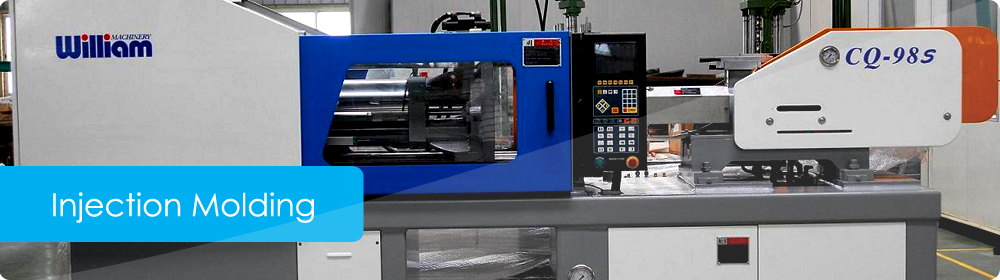
The most commonly used thermoplastic materials are polystyrene (low cost, lacking the strength and longevity of other materials), ABS or acrylonitrile butadiene styrene (a co-polymer or mixture of compounds used for everything from toy parts to electronics housings), nylon (chemically resistant, heat resistant, tough and flexible – used for combs), polypropylene (tough and flexible – used for containers), polyethylene, and polyvinyl chloride or PVC (more common in extrusions as used for pipes, window frames, or as the insulation on wiring where it is rendered flexible by the inclusion of a high proportion of plasticizer).
III) CAST FILM
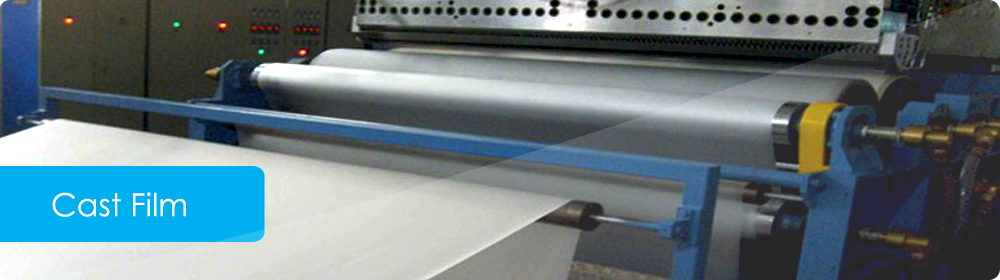
The extrusion of Cast Films by the flat die technique is becoming more and more important in view of its superior performance: throughput of more than 1 ton per hour against a few hundred kilogram’s per hour for the circular
die technique, and better control of the distribution of layer thickness in the transverse direction. As in the case
of bi-oriented films, the technique of multilayer co-extrusion allows for 3, 5 or 7 layers within complex structures.
The material temperature recommended for manufacturing is situated between 230 and 280°C when using a flat
die and between 180 and 210°C for a circular die, with water-cooling of the tubular film; higher temperatures
must be avoided as they may cause degradation of the additives. Cast polypropylene films are used for the
packaging of foodstuffs, textiles, the production of stationery, simulated leather goods, as well as for the manufacture of complex films by lamination or co-extrusion coating.
IV) INJECTION BLOW MOLDING
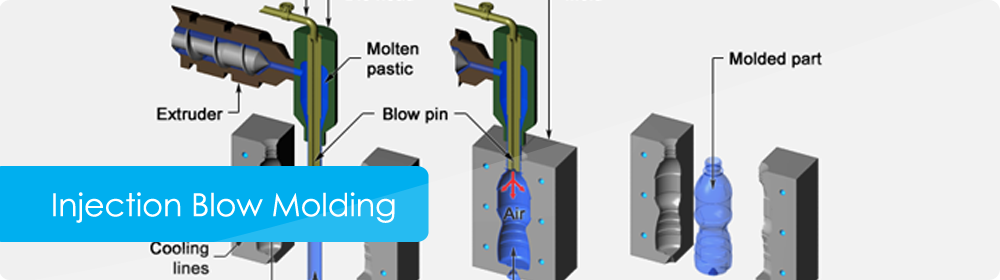
Injection Blow Molding is a process that combines traits of injection molding & blow molding and typically uses lower viscosity resins than those used in extrusion blow molding. Additionally, the process may be either a “onestep process” where the preform is molded on the same machine that it is blow molded on or, carried out using the “two-step process” where preforms are molded on an injection molding machine and then loaded into a second machine to be re-heated and inflated in the blow mold. Injection blow Molding is often preferred for small, complex bottles, such as those in medical applications.
V) EXTRUSION BLOW MOLDING
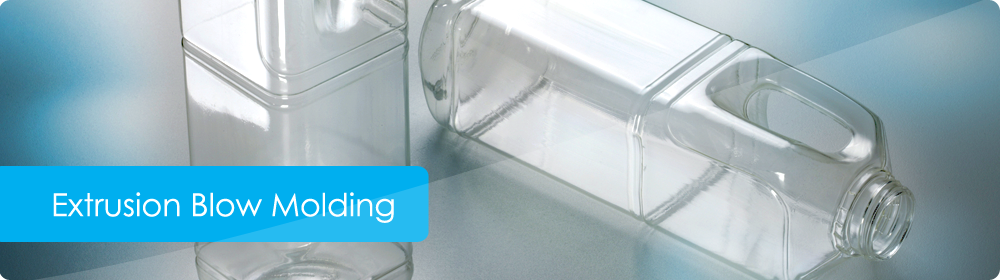
The Extrusion blow molding process begins with the conventional extrusion of a parison or tube, using a die similar to that used for making plastic pipe. To manufacture Plastic Bottles, industry uses a process known as Blow Molding. This process is used to manufacture hollow plastic bottles such as; milk jugs, shampoo bottles, bleach bottles, or any one of countless products you might see on store shelves. The plastic is fed in pellet form into the machines hopper, (this machine is known as a Blow Molder), and the plastic is conveyed forward by a screw inside a heated barrel being softened by both friction and heat. The softened plastic is then forced downwards through a circular die forming a hollow plastic tube called a “parison”.
The parison is then clamped inside a hollow mold and inflated from with-in. The air pressure forces the parison
to inflate against the mold surface, the plastic cools in the shape of the interior of the mold cavity. The mold then
opens and the plastic bottle is ejected. The bottle may they be conveyed on to trimming, printing and filling stations. Other processes for Blow Molding include Stretch Blow and Injection Blow. Extrusion blow molding can be used to process many different plastics, including HDPE, PP, PET and LDPE
VI) THERMOFORMING
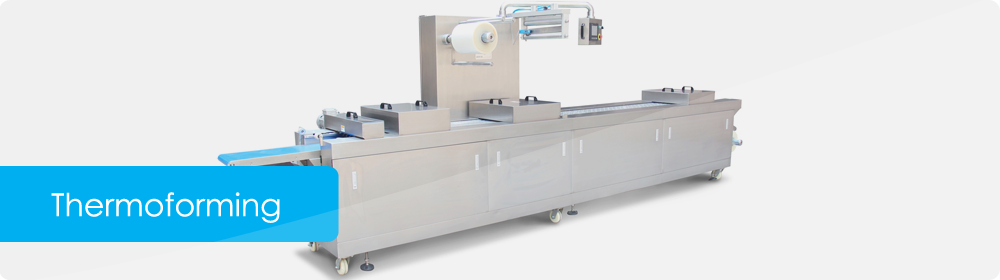
Thermoforming describes the process of heating a thermoplastic sheet to its softening point, stretching it over or into a single-sided mold, and holding it in place while it cools and solidifies into the desired shape. The thermoplastic sheet is clamped into a holding device and heated by an oven using either convection or radiant heat until it is softened. The sheet is then held horizontally over a mold and pressed into or stretched over the mold using vacuum pressure, air pressure, or mechanical force. The softened sheet conforms to the shape of the mold and is held in place until it cools. The excess material is then trimmed away and the formed part is released. Excess material can be reground, mixed with unused plastic, and reformed into thermoplastic sheets.
Thermoforming is commonly used for food packaging, but has many applications from plastic toys to aircraft windscreens to cafeteria trays. Thin-gauge (less than 0.060 inches) sheets are mostly used for rigid or disposable
packaging, while thick-gauge (greater than 0.120 inches) sheets are typically used for cosmetic permanent surfaces on automobiles, shower enclosures, and electronic equipment. A variety of thermoplastic materials can be used in this process, including the following:
> Low Density Polyethylene (LDPE)
> High Density Polyethylene (HDPE)
> Polypropylene (PP)
> Polystyrene (PS)
> Polyvinyl Chloride (PVC)
> Acrylic (PMMA)
> Acrylonitrile Butadiene Styrene (ABS)
> Cellulose Acetate
As mentioned above, there are different methods of forcing the thermoplastic sheet to conform to the mold. These
types of thermoforming include the following:
VACUUM FORMING: A vacuum is formed between the mold cavity and the thermoplastic sheet. The vacuum
pressure (typically 14 psi) forces the sheet to conform to the mold and form the part shape.
PRESSURE FORMING: In addition to utilizing a vacuum underneath the sheet, air pressure (typically 50 psi,
but up to 100 psi) is applied on the back side of the sheet to help force it onto the mold. This additional
force allows the forming of thicker sheets and creating finer details, textures, undercuts, and sharp
corners.
MECHANICAL FORMING: The thermoplastic sheet is mechanically forced into or around the mold by direct
contact. Typically, a core plug will push the sheet into the mold cavity and force it into the desired shape.
VII) WIRE & CABLES
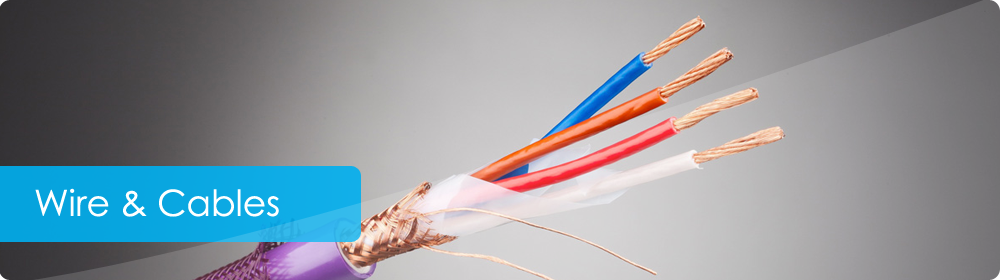
We provide total solutions for wire and cable industry with the ability to meet diverse global regulatory and product specifications. Our master batches are available for wide range of applications such as: Electrical wiring, House wiring, Telecom wiring, automotive wiring etc. We assure high quality standard, excellent dispersion with good electrical properties.
PRODUCTS:
- Antioxidant Master Batches
- Anti Rodent Master Batches
- Colour Masterbatches
- BLACK Masterbatches
- Flame Retardant Master Batches
- UV Masterbatches
VIII) ELECTRONICS

Blend Colours has the ability to develop unique and effective masterbatches for any electrical or electronic
applications. We are leading suppliers of specialized polymer materials with expertise in thermoplastic
compounds and colour and performance additives. We have the ability to develop unique and effective
combinations for any electrical or electronic applications.